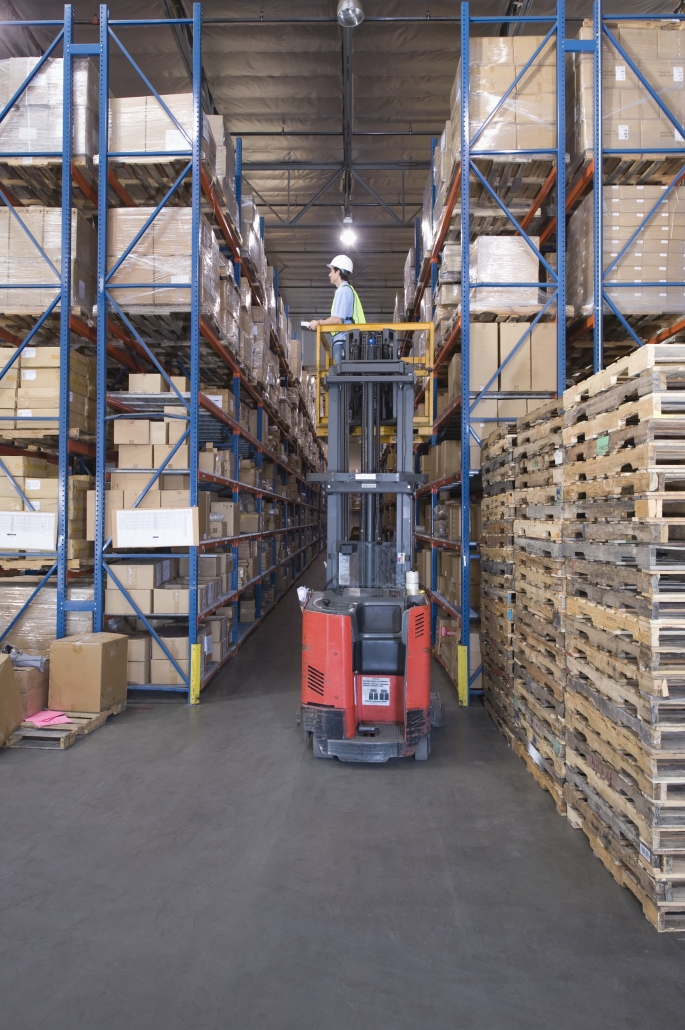
Rise Above: How Clear Heights & Racking Systems Revolutionize Warehouse Efficiency
In the dynamic world of industrial real estate, every inch of space matters. As goods move rapidly and storage requirements grow, the blueprint and setup of your warehouse becomes paramount. At the forefront of this space optimization exercise are clear heights and racking systems.
Simply put, the clear height of an industrial building is the distance from the floor to the lowest hanging obstacle, typically a structural beam or the roof. This is a critical measurement because it is directly correlated to your storage volume and equipment mobility. Taller clear heights allow you to store more products without expanding your footprint and enable the use of better, more efficient equipment.
Newer buildings typically have clear heights, ranging from 32 to 40 feet, compared to the 18 to 24 feet of older structures. New buildings are in limited supply and high demand which means you are going to pay a premium to get your hands on one, but the advantages are clear. Newer buildings have fewer constraints and can adapt to evolving technologies and equipment much easier. For the past few quarters, I have been talking about functional obsolesce and how these properties will struggle to find buyers and tenants in the future. Thus, if you own a building with an 18-to-24 foot clear height it has an element of functional obsolescence that negatively impacts its value.
Racking systems are the backbone of a well-organized warehouse. They transform vertical space into usable storage. Depending on your operation, there are many variations to choose from such as: selective racking, drive-in/drive-thru racking, push back racking and pallet flow racking. The optimal clear height paired with one of these racking systems can substantially boost operational efficiencies via increased storage, better inventory management and swift retrieval, which is especially helpful for those with high turnover. If you read my article on automation and robotics, you should have a good idea where I’m going with this. If your business is going to remain competitive between now and 2030, it would be wise to be incorporating these components into your operation now.
I realize that the initial outlay for state-of-the-art buildings and cutting-edge racking systems are not cheap. However, the dividends—both immediate and long-term—may justify the investment over the long-term. Not only do you gain efficiencies and remain competitive, but it often results in longer-term savings. Making use of the vertical space delays the need for physical expansion while efficient racking systems reduce the time spent on inventory-related tasks.
Grasping the intricacies of clear heights and racking systems transcends mere infrastructural knowledge. It’s a strategic gambit, a foresight into how your operations will evolve. By judiciously pairing height with racking, you set the stage for space optimization, operational efficacy, and sustained productivity. This proactive approach is pivotal to staying relevant and competitive in our ever-changing industry.
Did You Find This of Value? Make a Tip:
Bitcoin: bc1qpvm8pyflhvp3laxllsm98kskynas7eclh07dfz