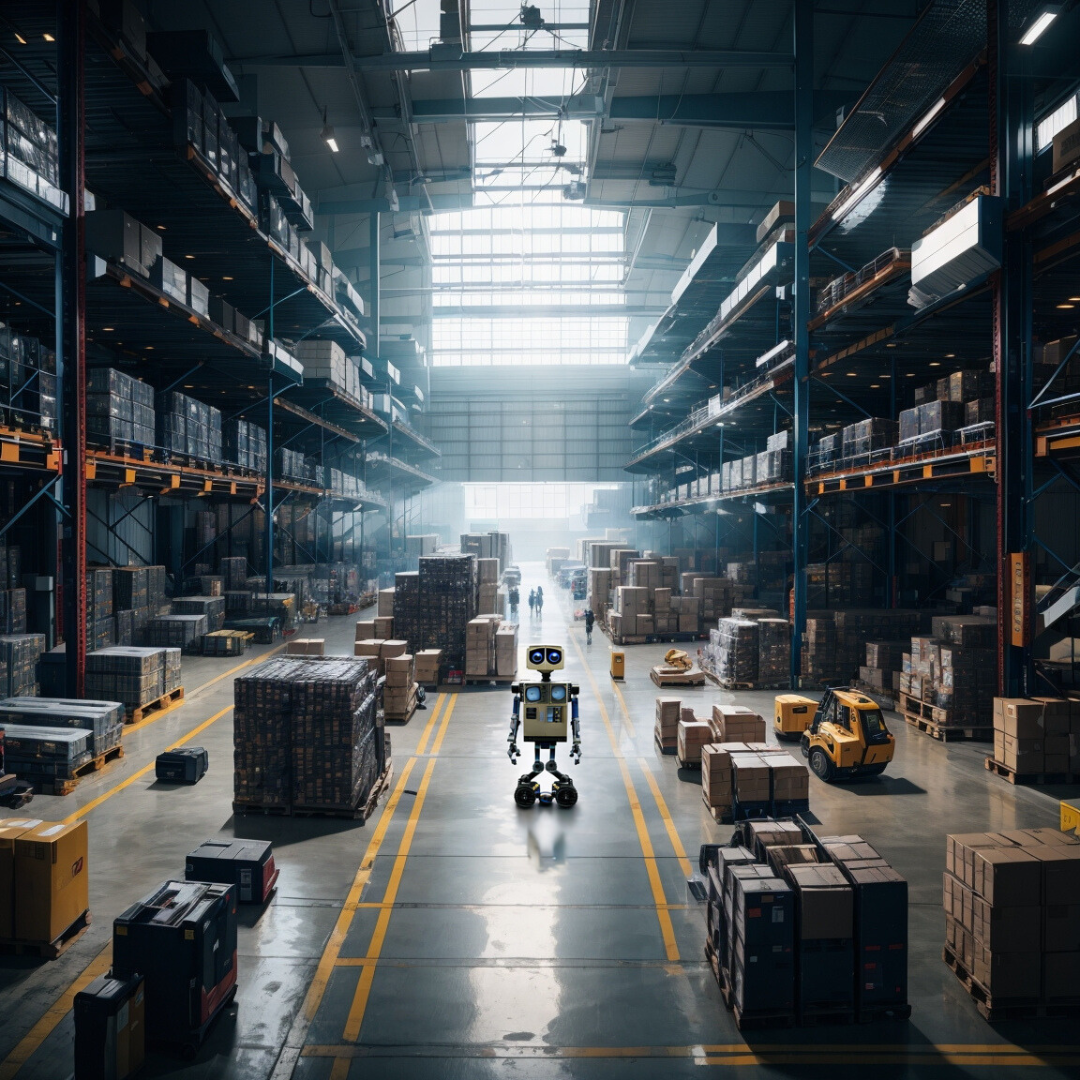
Embracing the Robot Revolution: Navigating Automation & AI in Industrial Real Estate
Automation, robotics, and artificial intelligence (AI) have been transforming industries across the globe, and the industrial real estate sector is no exception. As technology continues to advance rapidly, businesses and investors in the industrial real estate space need to stay informed about the current landscape and plan for the future. In the US alone, the industrial real estate market encompasses about 20 billion square feet, valued a little over $2 trillion. It’s a massive industry with a lot of opportunity for optimization and technological modernization.
In my experience, those who typically benefit the most are the direct-to-consumer businesses (think e-comm) because they have a lot of SKUs to choose from and the units per order is much higher. Selecting all those items from different areas is time consuming and labor intensive. There is no shortage of FUD around this topic and most overlook the fact that the adoption of these technologies is tackling two major issues in our society—labor shortages and productivity. As labor costs continue to rise, businesses are turning to automation to mitigate expenses and increase productivity. Afterall, robots don’t take lunch breaks, call in sick, or stop working after an 8-hour shift. They don’t negotiate their salary or take vacations. It is a massive productivity increase, something we need very badly. Don’t believe me? Look at Amazon—As of today, 30% of Amazon’s workforce are robots and I have a difficult time seeing a scenario where that percentage does not grow over time.
For the small business owner who is focused on running the business, exploring all the various options can be a daunting and overwhelming task. The reality is it does not have to be. Start by auditing your current operation. Where is your bottleneck? How old is the racking system? Are you using a palette jack and forklift to move things around? Is it a throughput or labor issue? Make it easy on yourself and back into the issues you want to solve. Consider replacing paper picking techniques with various scanning, voice & lighting systems so your employees are more hands-free, and things keep moving resulting in better productivity. These are technology solutions. The automation solutions include warehouse management systems (WMS), pick to light systems, conveyor systems, and autonomous mobile robots (AMRs). These technologies streamline operations, reducing errors, improve efficiency and provide data instantaneously! Simply reducing the number of errors will have an immediate impact on the bottom line while data on demand enhances forecasting accuracy and improves decision-making processes.
When considering these types of upgrades, business owners and investors alike, must understand the technological requirements relative to the physical limitations of their property. For example, industrial buildings should be equipped with infrastructure to support automation and robotics, such as adequate power supply, advanced material handling systems, and high ceilings for vertical storage. As these changes take place, legacy businesses and properties unwilling to adapt will face major challenges. Certain businesses will no longer be viable acquisition targets and the functionally obsolete properties will lose value and struggle to find tenants and buyers while properties with flexible layouts and adequate infrastructure will be in high demand.
These changes will not occur over night; however, the secular trend is already in motion and will not slow down. There are a lot of options available today and will continue to evolve over the next three years. If you are involved in industrial real estate, you should explore the following solutions:
- Warehouse Automation: Automated material handling systems, conveyor systems, and robotic arms can streamline warehouse operations, including order picking, sorting, and packing.
- Autonomous Mobile Robots (AMRs): AMRs are intelligent, self-navigating robots that can move within warehouse environments to transport goods, retrieve inventory, and perform repetitive tasks.
- AI-Driven Inventory Management: AI-powered systems can analyze historical data, demand patterns, and market trends to optimize inventory levels, reduce stockouts, and enhance supply chain visibility.
- Predictive Maintenance: AI algorithms can monitor equipment and machinery, predicting maintenance needs and reducing downtime. Predictive maintenance can prevent costly breakdowns and optimize asset utilization.
Automation, robotics, and AI are revolutionizing the industrial real estate sector, presenting both challenges and opportunities for businesses and investors. Staying informed about the current landscape and planning for the future are essential for success in this rapidly evolving environment. If you are interested in learning more, I would be happy to continue the conversation and even connect you with providers and consultants that specialize in this arena.
Did You Find This of Value? Make a Tip:
Bitcoin: bc1qpvm8pyflhvp3laxllsm98kskynas7eclh07dfz